Installation Prep for New Equipment
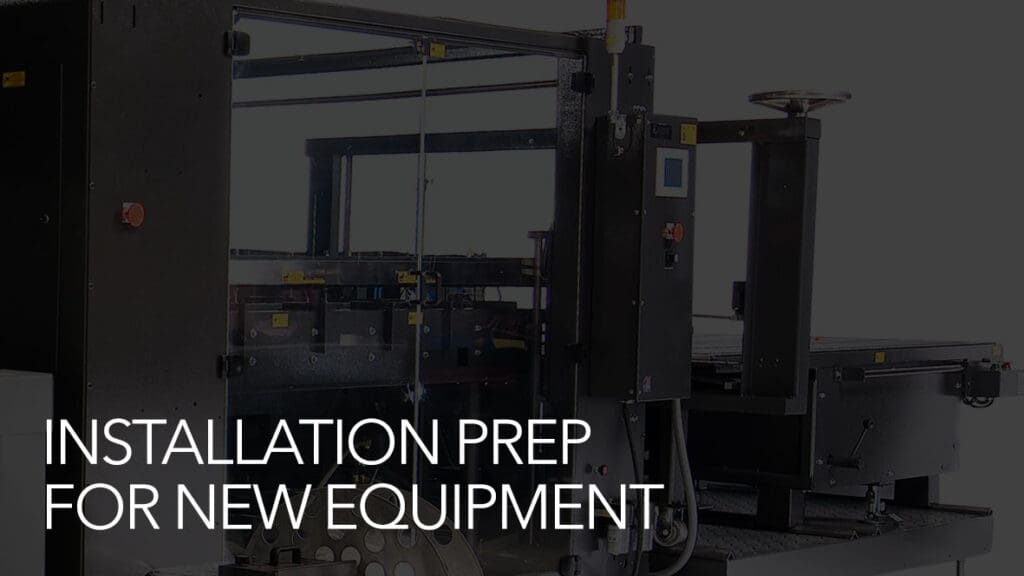
Purchasing new equipment for your facility is an exciting venture and can be a sign of growth for your company. But what can be done in preparation between that purchase and when the equipment arrives on a facility floor? In this blog, we discuss how you can plan for the new equipment’s arrival, how you can prepare your employees, and what to do once the equipment is in place.
Creating a Plan
It is important to conduct as much research as possible in the early stages of adding or replacing equipment in your facility. You will want to survey the current space where you are looking to place the new equipment.
Key Questions:
Can the area support the weight of the new equipment? Is the foundation level where the equipment will be placed?
It is important to check the foundation for cracks that could impact the new equipment and the structural integrity of your facility. For example, having a floor that is not level could affect how the equipment sits on the production floor and affect the performance of the machinery. Fixing this issue could take time but will benefit you in the long run.
If you are replacing equipment, is there enough space for the new machine? If not, where is the best location to install it while not interrupting the flow of the facility?
When researching new equipment, size and location are two important factors. Many companies have equipment similar in functionality but can vary in size. If a specific brand of equipment appeals to you and your company, consult with their sales team to assist you with purchasing and placing the new machine. Dimensional drawings of the new equipment will help decide if and where the new equipment will fit.
Are your employees ready for the changes? Would their insight be helpful?
Informing your team of potential changes to the production floor is vital. Individuals working on the production floor would be interacting with the machine the most. Scheduling time for them to be trained on how the machine operates is key. From starting it up to shutting it down, every piece of information is valuable. Many companies offer hands-on training sessions when installing new equipment.
Is there an installation and delivery plan?
On the day of delivery, it is good to have a plan in place for smooth installation. Some factors to consider are:
- Which part of your facility will the equipment be brought in?
- Will your production have to be shut down during the day, or will the equipment be brought in after-hours?
- Will a forklift be needed to move the equipment around the production floor?
- Will weather impact the delivery or installation?
- Will the installation be on a different day than when it is delivered?
- Is there a clear path to the installation area?
- Are there any special electrical or air requirements the equipment requires?
These are some of the questions that your team needs to ask to ensure that the delivery and installation go as smoothly as possible. This process can be stressful, but having a plan to make sure your team is the most prepared they can be, it can go off without a hitch!
Eastey offers installation and setup services for each piece of large equipment we sell. Our team of knowledgeable packaging sales professionals will help you find the packaging machinery that will work best for your packaging line and your facility. Visit our website to view our full line of packaging machinery designed to help customers deliver their products to the world.