Common Questions about Eastey’s Packaging Equipment
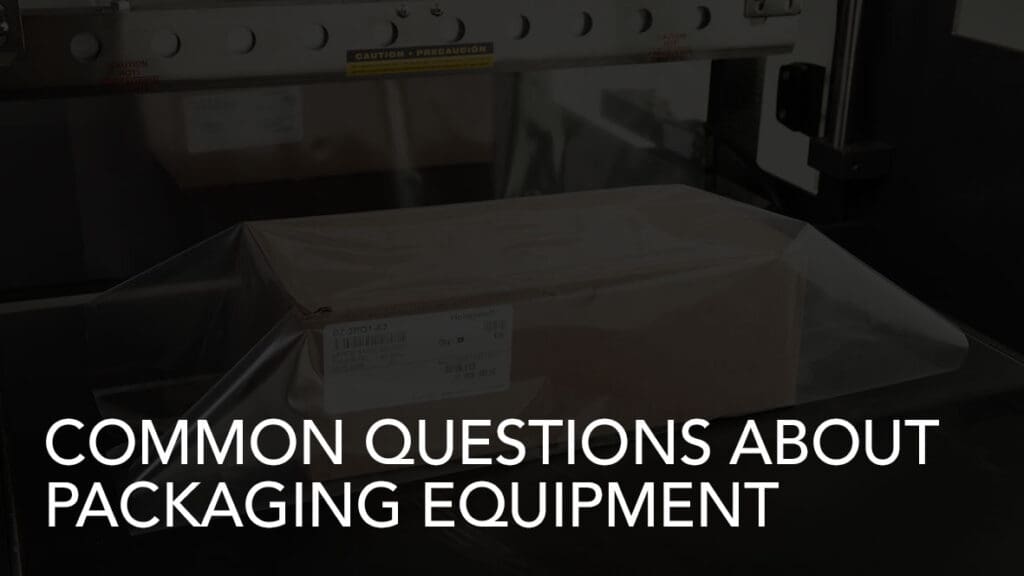
Eastey continues to add more packaging solutions to its product line. You may already know the ins and outs of many of our packaging machines, but some may not be as familiar. This blog examines Eastey’s product line and provide details about when and where to use these packaging products.
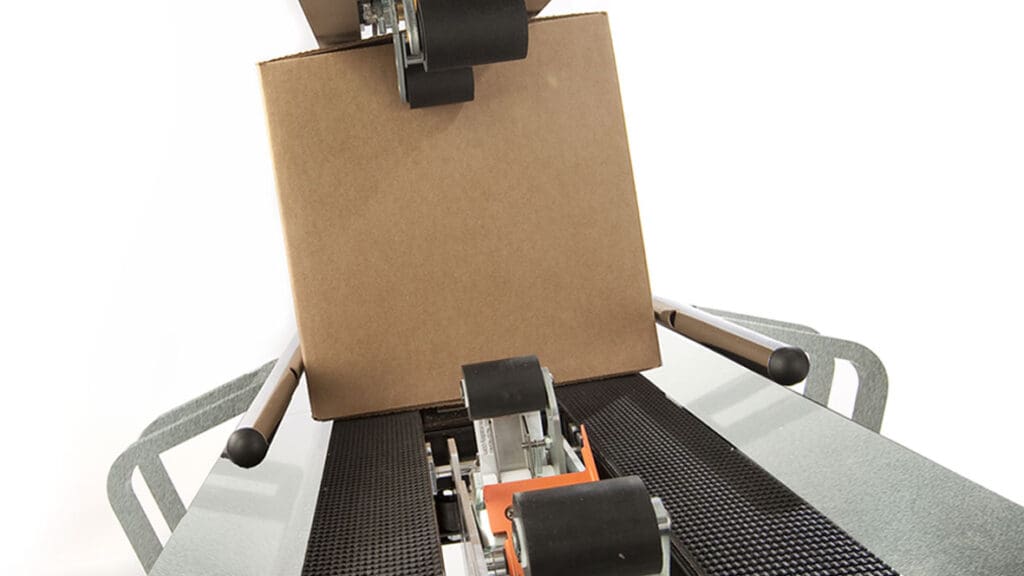
Case Tapers
What are the different types of case tapers?
The first case taper family that we will discuss is our line of uniform semi-automatic case tapers. Uniform semi-automatic case sealers are commonly found in operations with product runs using the same box size. These sealers require the operator to fold the box flaps and introduce the case into the machine. A fully automatic uniform case taper may be the solution if more automation is required. Uniform fully automatic case sealers are also used for runs of the same box size; however, fully automatic sealers do not require an operator to fold the case flaps.
A random semi-automatic case taper may be needed when an operation has product runs with various box sizes. Random semi-automatic tapers still require the operator to fold the case flaps before introducing the case into the machine, but the semi-automatic sealer will automatically adjust to various case heights and widths.
Why do some tapers have a bottom belt, top and bottom belt, while others have a side belt?
Most case sealers use belts made of a rubber-type material to drive the cases through the machine. The belt drives on a case sealer can vary in position (bottom, side, top and bottom) depending on the box application. These factors include the size and weight of the case being sealed. For example, oversized, lightweight, or void-fill cases work better with a side belt-driven case taper than a bottom belt-driven sealer. Bottom belt case sealers rely on a filled case where the product supports the box as it passes through the sealer.
Another type of sealer is the top and bottom-driven sealer. Top and bottom sealers utilize four belts – two on the top and two on the bottom, to help drive the case through the sealer. Top and bottom belt machines are ideal for tall and narrow cases that tend to be heavier.
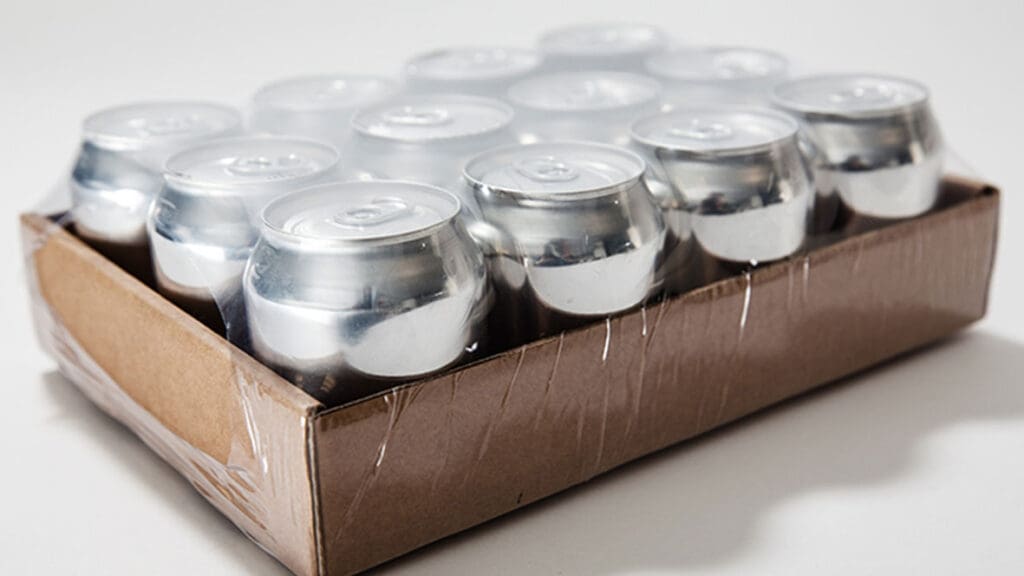
Shrink Wrapping and Shrink Bundling
What is the difference between shrink wrapping and shrink bundling?
Although there are similarities, there are major differences between the two. Shrink bundling is commonly used more for function than appearance. Usually wrapped in heavier gauge polyethylene film, products can be sealed in a loose unsupported package or sealed in trays or cases. This sleeve wrapping is often seen on multi-pack beverage products such as water bottles, trayed products, multi-pack consumer goods, cases that need extra security, and other larger products bundled in a group.
Bundled products are typically sealed with open ends on both sides. These open ends typically form a circular or oval shape, which is why they are often referred to as a “bullseye” enclosure.
Shrink wrapping, on the other hand, is commonly used for individual or small multi-pack applications. This machinery differs from bundling due to the film’s lower gauge or mil thickness commonly used in shrink wrapping applications, as well as the seal bar’s shape. L-bar sealers have L-shaped seal arms instead of the single seal bar found on bundlers. Eastey’s L-bar sealers are great for positive sealing a wide variety of films, including polyolefin, polyethylene, and PVC. These machines seal various products ranging from food and beverage to building products and household goods. Depending on the application, L-sealers can also be supplied as an automatic machine or as an L-sealer and tunnel combined on a common frame.
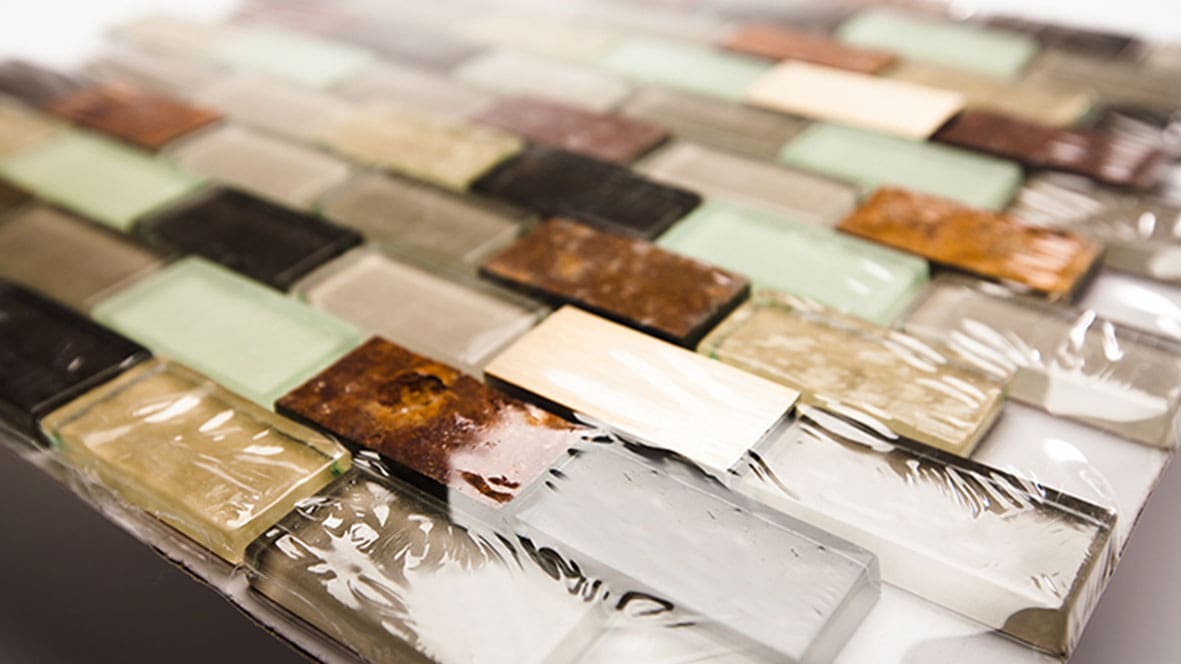
Shrink Tunnels
Your products are wrapped or bundled; what’s next? Shrink and bundling tunnels are used after a product is wrapped in film to shrink the film, resulting in a clean and tight package. Shrink tunnels and bundling tunnels also differ from one another. Shrink tunnels are designed for smaller and lighter products, and the film thickness used in L-sealer applications is typically lighter weight. The tunnel opening is also smaller than a bundling tunnel opening. Bundling tunnels have a bigger tunnel opening and overall size when compared to shrink tunnels. The increased size is due to the larger heating banks in the tunnel that are needed to shrink the heavy gauge film used in bundling applications.
Eastey also supplies other packaging solutions designed to help customers meet the demands of their product lines. These solutions include case erectors, carton formers, belt conveyors, gravity fed conveyors, accumulation tables, strappers, and more.
Visit our website and product pages to learn more about Eastey’s full line of packaging equipment!